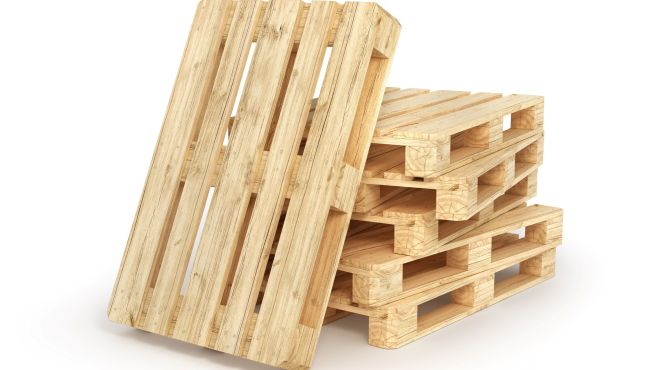
Carrying on the theme of innovation and continuous improvement, the teams at our six North American plants are constantly looking for new ways to improve upon their overall operational efficiency. From machinery and equipment upgrades to basic process improvements, our plants seek any and every opportunity to better serve our valued customers.
This mindset is not lost when it comes to our group-wide focus on the environment. Despite our film-first mentality, sustainability initiatives at IEF don’t just stop at our products. A recent improvement initiative by our Prattville location proved that sometimes it’s the little things that can make a huge difference. Buying back hard-to-recycle packaging items from our customers to free up tons of valuable space in landfills? That’s the kind of thinking we applaud here at IEF. In our first Plant Promo, we’re taking a trip down to Prattville, Alabama to see how some innovative thinking and customer collaboration is helping us reduce our overall environmental footprint.
Pallet Problems?
It's fair to say that most don’t think of wooden pallets, end boards, or core plugs when considering the potentially environmentally-unfriendly byproducts of plastic manufacturing. These products are generally very durable, highly-recyclable, and can be reused several times over, but often find themselves improperly recycled or disposed of in landfills at the end of their lives. As a leading producer of blown film, one can imagine how much of these packaging materials the IEF Prattville plant goes through on a monthly basis.
To combat this issue, the team in Alabama reached out to a customer of ours who we ship to on a regular basis to propose a “buy back” recycling program for the packaging supplies. Led by Plant Manager Stephen Hyer, the Prattville team collaborated with the customer to create an effective two-way stream of communication. According to Hyer, “After receiving and unpacking the shipments of film, the customer sorts and neatly stacks the left-over pallets, end boards, and core plugs, rather than disposing them into the dumpster or landfill. When they have enough materials or we are running short, our plant reaches out to them to buy back the packaging supplies.”
While there’s no way to know for sure what would happen to these packaging materials under normal circumstances, the creation of the “buy back” program ensures the materials will be reused and have their lives extended – freeing up valuable landfill yardage.
Hyer stated that aside from the environmentally-friendly benefits, the program has “helped further strengthen our communications with the customer in all areas, ultimately improving our relationship all together.”
Sticking with Sustainability
Aside from the “buy back” recycling program, the IEF Prattville team prioritizes sustainable operations on a daily basis. As a partner in Operation Clean Sweep, the Prattville operation is constantly focused on pellet loss and control. Led by multiple IEF and Inteplast Group-led initiatives, IEF Prattville strives to achieve zero pellet loss on a daily basis, minimizing potential leakage from the plant into the ecosystem. Additionally, the Prattville team has made large strides in their abilities to collect, recycle, and reuse trim scrap, while also emphasizing sustainability-focused employee and operator training.
When asked what sustainability at the plant level means to him, Hyer stated the following:
“Sustainability means controlling every pellet, core, packaging item, and piece of trash we produce. We must recognize where we can recycle and reuse and take advantage of that daily. Anytime we can prevent something from leaving the plant in an unproductive way, it is a win.”
To learn more about our sustainability initiatives at our plants, or for information on our InteGreen™ family of sustainable films, click here.
Published May 2021