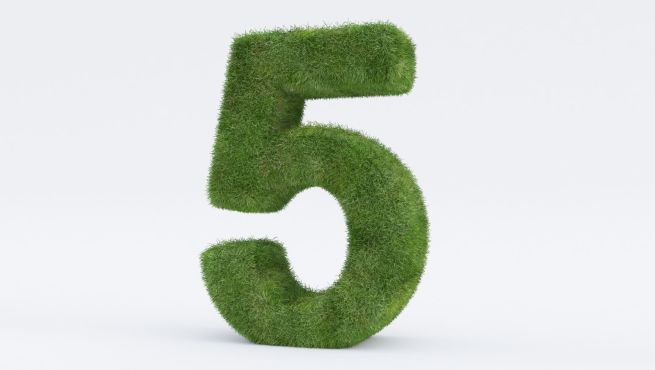
As a leading North American supplier of polyethylene films, we feel that it is our responsibility to educate our customers, and the public, on how to make their plastic packaging more sustainable. At IEF, we manufacture a variety of environmentally-friendlier plastic films that can help reduce the potential for negative environmental impacts associated with the improper disposal of plastic products. In recognition of Earth Day 2022, let’s take a look at 5 ways to help make flexible plastic packaging more sustainable.
1. Recycled Content (PCR and PIR)
The demand for recycled content in packaging has exploded in recent years. Both post-consumer (PCR) and post-industrial (PIR) recycled content have been embraced as great options to help reduce the amount of virgin resins used in plastics production.
Recycled resins are made from recycled plastic products that are re-pelletized to be re-used in the manufacturing process. PCR comes from recycled consumer products, such as water bottles or recycled plastic bags, while PIR comes from materials used in industrial applications.
Recycled resins can be incorporated in various amounts in the blown film manufacturing process, which helps to close the circular economy loop by providing a home for collected recycled materials.
Additionally, the increased use of recycled content helps reduce the total amount of virgin materials being utilized, which means less opportunities for discarded plastics to wind up in landfills or as environmental leakage. To learn more about PCR and PIR, click here.
2. All-PE Recycle-Ready Films
A common misconception with plastic products is that they are not recyclable – a claim which is simply not true. In fact, plastics and plastic products have become increasingly more recyclable over the years, and recycling infrastructure has sprouted up globally to help match demand. In the US alone, approximately three million tons of plastic materials were collected for recycling in 2018, and this number is projected to continue to grow.
When it comes to recyclable films, many single-material films are currently accepted in curbside and Store Drop-off recycling streams. IEF produces a variety of all-PE film structures that when utilized correctly can be recycled in most US store drop-off recycling programs.
For more information, reach out to your local technical expert today.
3. Compostable Films
A relatively new technology, compostable plastic films offer an innovative solution to the inherent longevity of plastics that can become problematic when improperly disposed of.
Often utilized in highly specialized applications – compostable films are available with both home and industrial compostable degradation capabilities.
Looking for an example of compostable films in action? Check out this case study on compostable fruit labels.
4. Multi-Material Compatibilizers for Recycling
We previously covered how many single-material films are store drop-off recyclable, but what about multi-material constructions? For the most part, standard off the shelf multi-material plastic films are extremely difficult to recycle – and often are not recyclable at all. These products require advanced recycling infrastructure capable of separating the different materials into different recycling streams.
However, recent technologies have been developed, called compatibilizers, which when utilized correctly allow for multi-material film constructions to be collected and recycled via in-store drop-off programs. With this new technology, previously non-recyclable co-extruded PE films featuring materials such as EVOH or nylon can be successfully certified for various recycling programs where accepted.
Check out our new InteGreen™ Store Drop-off Recycle-Ready barrier films, which feature EVOH-compatibilized materials.
5. Downgauging/Source-Reduction
While the use of recycled content helps to reduce the amount of virgin materials being produced, another option is to seek opportunities for downgauging or source-reduction.
Downgauging is the process of re-engineering a film’s design to lower the overall gauge. While this process is often used to lower costs, there is also a significant sustainability-focused benefit due to the reduction of required source materials.
Depending on the application, our technical team can work directly with our customers to examine their existing film to determine if there is an opportunity to downgauge.
Check out some of our case studies to see real-world examples of downgauged projects, or reach out for more information.
Interested in receiving the latest IEF and flexible packaging industry news delivered straight to your inbox? Subscribe to the Roll Call, our free monthly e-mail newsletter.
At IEF, It's About the Film.
Published April 2022